Air compressors are used to power a variety of tools and machines, and the choice of oil-injected or oil-free models can have a significant impact on the performance of the compressor.
This article examines the differences between oil-injected and oil-free air compressors, exploring the benefits and drawbacks of each type. It also provides guidance on the best type of air compressor for different applications.
With this knowledge, you can make an informed decision when selecting an air compressor for your needs. Read on to find out more and discover the perfect air compressor for your project.
Oil-Injected Vs. Oil-Free Air Compressors
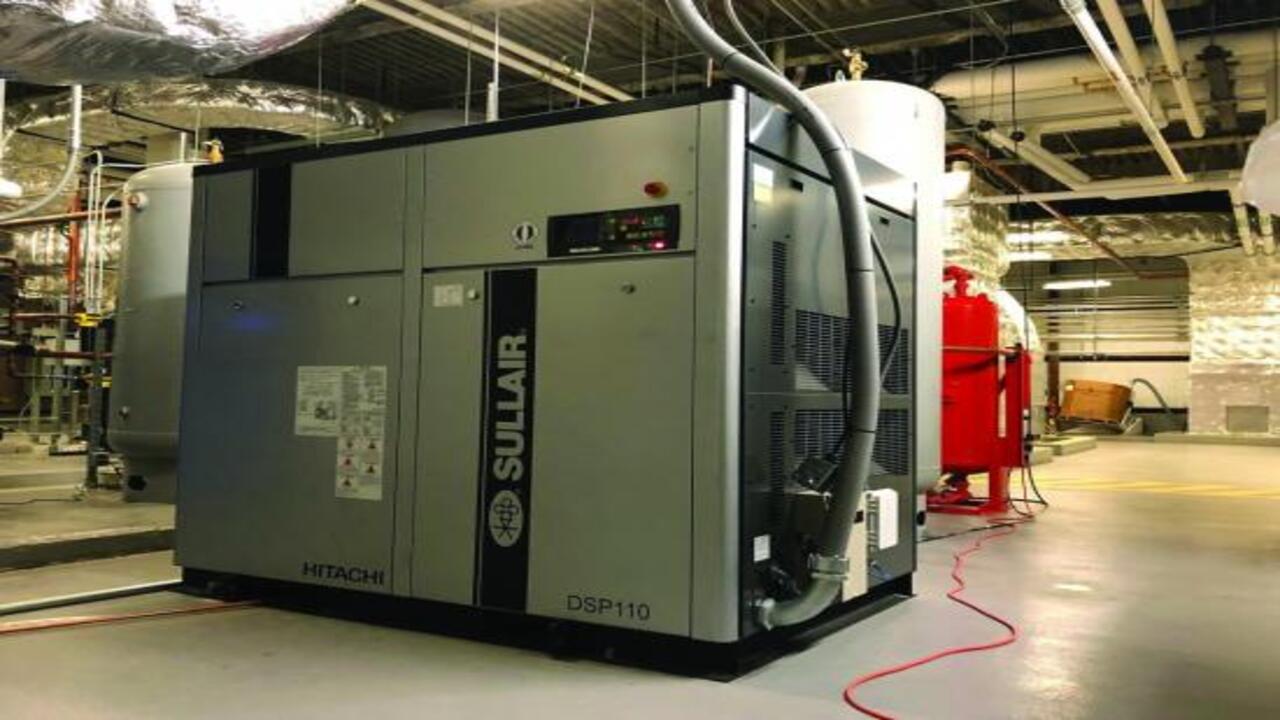
Before diving into the details of oil-injected air compressors versus oil-free air compressors, it is important to understand the basics of air compressors. Air compressors are machines that use mechanical energy to compress air and store it in a tank for later use.
This stored air can be used for a variety of purposes, such as powering pneumatic tools, inflating tires, and powering paint guns. Now, the question is, which type of air compressor should you choose: oil-injected or oil-free? In this article, we will discuss the differences between oil-injected and oil-free air compressors and their respective advantages and disadvantages.
Advantages Of Oilinjected Air Compressor
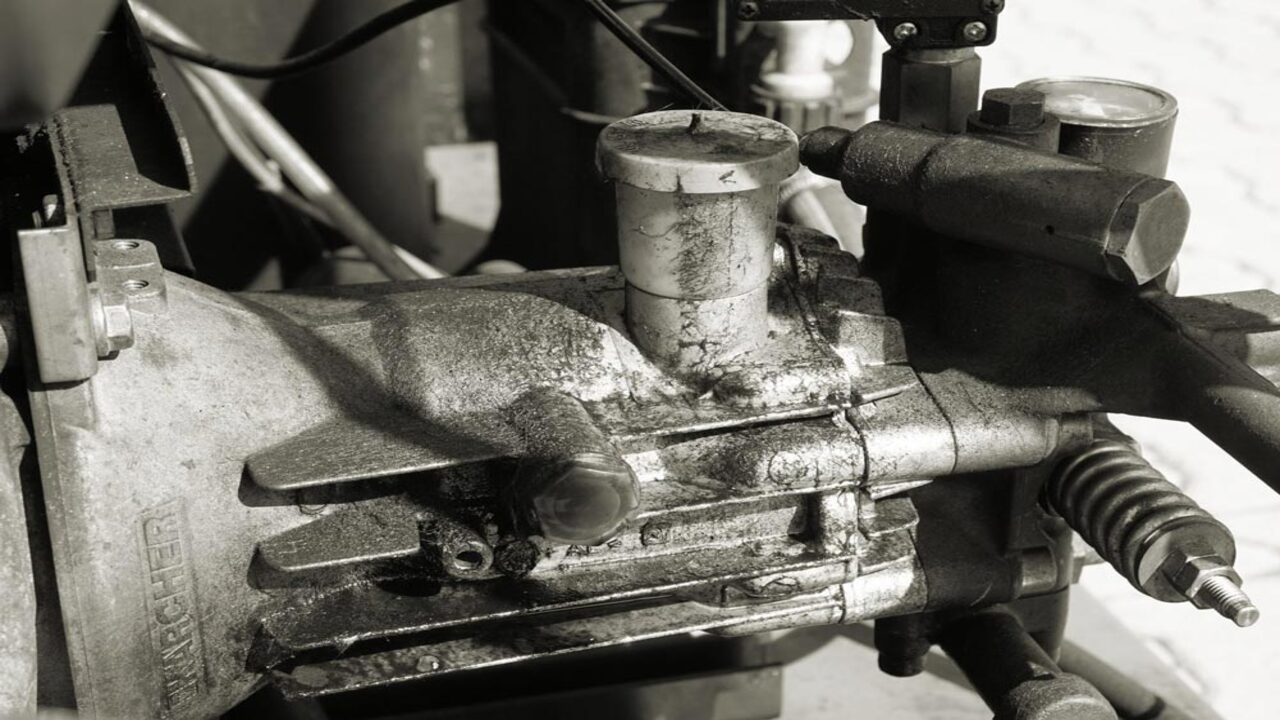
Oil-injected air compressors are advantageous because they can handle higher pressure levels than oil-free models. They can also handle heavier workloads and operate more efficiently. Additionally, the oil helps to lubricate the components, which can help reduce wear and tear on the system. Furthermore, they don’t require frequent maintenance and can last for years with regular servicing.
The oil also helps to reduce noise levels and keep the system cool. Finally, oil-injected air compressors are generally more cost-effective than oil-free models. This is because they require less maintenance and can run for longer periods of time without needing to be serviced or replaced.
Longevity
When it comes to the longevity of an air compressor, oil-injected models tend to last longer than oil-free models. This is largely due to the fact that the oil provides an extra layer of protection from wear and tear. The oil-free models are often made with lower-grade materials, and are less durable than oil-injected models.
Additionally, oil-injected models are regularly serviced and maintained, which can help them to last longer than their oil-free counterparts. However, oil-free models are still suitable for short-term use, and may still last a long time. Ultimately, it comes down to your needs and how often you plan to use the air compressor.
Lower Maintenance
When it comes to lower maintenance requirements, oil-injected air compressors are the clear winner. This type of air compressor has an oil reservoir that lubricates the motor and piston, which helps to reduce wear and tear on the parts. Plus, the reservoir has a filter that needs to be changed periodically to keep the air compressor running efficiently. On the other hand, oil-free air compressors do not require any lubricating oil or filter changes.
While this may seem like an advantage, it can actually lead to more frequent maintenance needs. Without oil to lubricate the parts, the air compressor is prone to wear and tear, which can require more frequent repairs.
Greater Efficiency
When it comes to efficiency, oil-injected air compressors are often considered to be the more efficient option. This is because they are designed to use the oil to lubricate the parts, which makes them run more smoothly. Additionally, the oil helps to cool the parts, which further increases the efficiency of the compressor.
This type of compressor also usually has a higher output pressure than an oil-free compressor, which makes it more suitable for certain uses. However, oil-injected compressors require more maintenance, as the oil needs to be changed regularly.
Lower Operating Costs
When it comes to operating costs, oil-injected air compressors are generally less expensive than oil-free air compressors. Oil-injected compressors require less maintenance and less frequent oil changes, which can save time and money. The cost of the oil itself is also cheaper than the cost of oil-free compressors.
Furthermore, oil-injected air compressors don’t require the same level of skilled maintenance to keep them functioning properly, making them an attractive option for businesses that don’t want to invest in specialized staff.
Oil-free air compressors require more frequent maintenance and more frequent oil changes, which can drive up operating costs significantly. They also require more specialized staff to keep them running correctly, adding to the overall cost of operation.
Disadvantages Of Oilinjected Air Compressor
Oil-injected air compressors have several drawbacks. The first is that they require regular maintenance and oil changes. The oil used to lubricate the compressor must be changed periodically to ensure its efficiency and to prevent it from becoming contaminated.
This can be costly and time consuming. Additionally, oil-injected compressors are often louder than their oil-free counterparts. They can also be more expensive to purchase initially. Lastly, they are not as energy efficient as oil-free models, so they can lead to higher energy costs.
Initial Investment
When it comes to air compressors, one of the main considerations for any buyer is the initial investment. Oil-injected compressors require a larger upfront investment than oil-free models. This is because oil-injected models tend to have more features and can generate more power.
On the other hand, oil-free compressors are generally less expensive and are easier to maintain. If you’re looking for a compressor that will last for years, then the oil-injected model may be the way to go. However, if you’re on a budget and need a compressor for occasional use, then the oil-free model may be the better choice.
Both models require different maintenance schedules and can vary in price depending on the size and power of the compressor. It’s important to research both models before making a purchase to ensure that you get the best compressor for your needs.
Risk Of Oil Contamination
Oil-injected air compressors come with certain risks of oil contamination that are not present with oil-free air compressors. Oil can enter the air stream from the compressor, contaminating it with particles that can damage downstream equipment.
This can happen when the piston rings are worn and oil escapes into the air stream, or if the oil is not replaced often enough. Additionally, if the oil isn’t changed regularly, it can become acidic, leading to further corrosion of the compressor.
To avoid this risk, oil-injected compressors must be regularly monitored and maintained. Oil-free air compressors, on the other hand, don’t use oil, eliminating any risk of oil contamination. They also typically require less maintenance than oil-injected compressors, saving time and money.
Oil-free air compressors may be a better choice for businesses where the potential for oil contamination can’t be tolerated.
Risk Of Oil Leakage
When deciding between an oil-injected air compressor and an oil-free air compressor, an important factor to consider is the risk of oil leakage. Oil-injected air compressors use oil to lubricate the components, which means there is a greater risk of oil leakage.
On the other hand, oil-free air compressors use synthetic lubricants that do not require oil changes, and therefore do not pose the same risk. Oil-injected air compressors also require more maintenance than oil-free compressors, as the user must regularly check for signs of oil leakage and replace any worn or damaged parts.
Additionally, oil-free compressors are generally more efficient than oil-injected compressors, as they do not have to overcome the resistance created by the oil. Overall, while oil-injected air compressors may initially be cheaper than oil-free air compressors, in the long-run, the cost of repairs and maintenance can outweigh any initial savings.
More Complex Operation
When it comes to more complex operations, oil-injected air compressors offer more advantages than oil-free models. They have higher compression ratios, meaning they can generate more air pressure with less input power.
This makes them ideal for applications where pressure is essential, such as sandblasting or running pneumatic tools. Additionally, oil-injected models are also more durable and require less maintenance since they have fewer moving parts.
On the other hand, oil-free compressors are designed for applications where clean air is a necessity, such as medical applications or food production. As such, they are often more expensive than their oil-injected counterparts. Ultimately, it’s important to consider the application you are using the compressor for when making a decision.
Advantages Of Oilfree Air Compressor
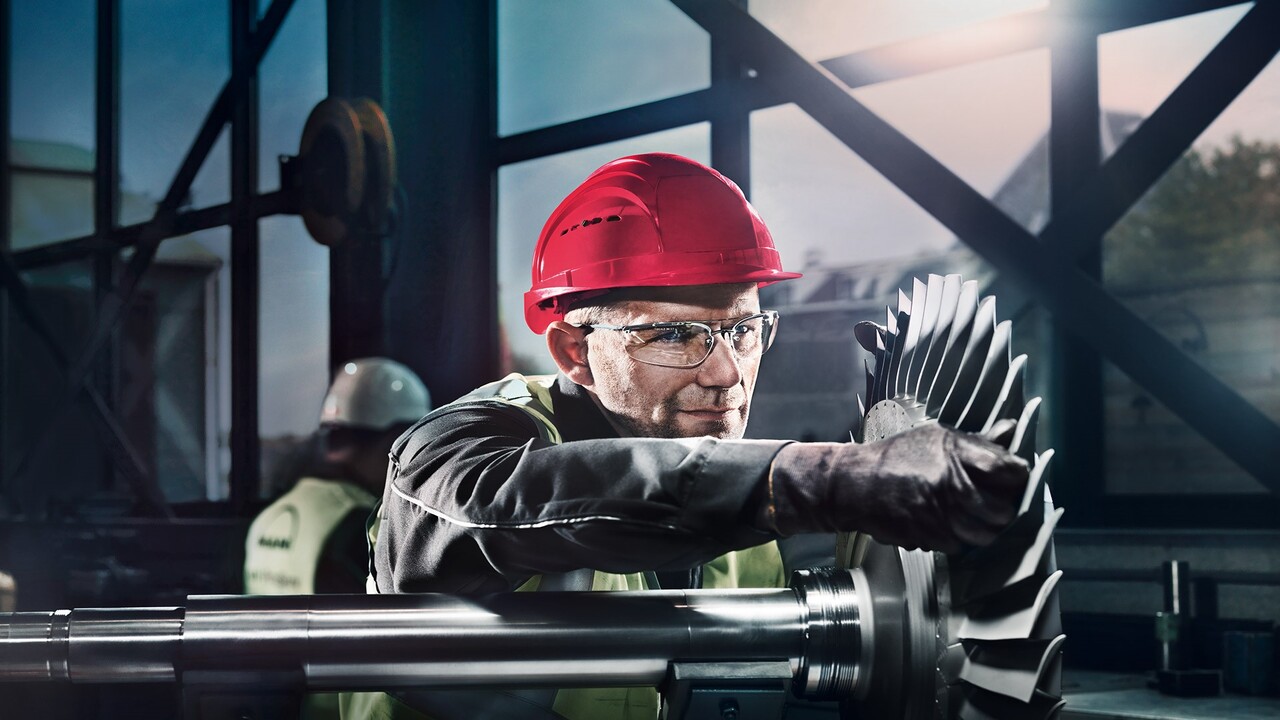
Oil-free air compressors offer a range of advantages over oil-injected models. They are generally quieter in operation, require little to no maintenance, and produce an uncontaminated air supply that is ideal for applications such as spray painting and medical use.
Additionally, oil-free air compressors are often more portable and more energy efficient than oil-injected compressors. Maintenance and service costs are also reduced due to the lack of oiling required. Furthermore, oil-free air compressors are better for the environment, as they produce fewer emissions and consume less energy.
The elimination of oil also removes the risk of oil contamination in the compressed air supply. Finally, oil-free air compressors are generally more reliable than their oil-injected counterparts, as there are no oil filters or other components that may need regular maintenance or replacement.
Cheaper Initial Investment
When choosing an air compressor for a business, the initial investment cost of the device is a major factor. Oil-injected air compressors tend to be the more affordable option, making them a great choice for budget conscious buyers.
The initial cost of the device includes the cost of the compressor and any additional parts, such as a tank, motor, and filter. Additionally, oil-injected air compressors tend to require less maintenance, meaning the overall costs of ownership may be lower when compared to oil-free models.
The downside of oil-injected air compressors is that they generally need to be replaced more frequently than their oil-free counterparts due to the need to replace oil. Therefore, the overall cost may be higher in the long run.
No Risk Of Oil Contamination
When it comes to air compressors, the debate between oil-injected and oil-free models can be quite heated. The main difference between the two is that oil-injected air compressors use oil to lubricate the internal components, while oil-free air compressors use synthetic lubricants or Teflon. The main advantage of an oil-free air compressor is that there is no risk of oil contamination.
The synthetic lubricants used in oil-free air compressors are designed to last longer than traditional oil, meaning that they do not need to be replaced as often. Moreover, since the lubricants are synthetic, they are resistant to temperature variations and will not break down as quickly as traditional oil. This means that oil-free air compressors require less maintenance over time and are less likely to suffer from wear and tear.
Low Maintenance Costs
When it comes to air compressors, low maintenance costs can be a major deciding factor. Oil-injected air compressors have a higher maintenance cost than oil-free air compressors due to the additional lubrication requirements. Oil-injected compressors require regular oil changes and the lubrication system must be regularly inspected and maintained.
Oil-free air compressors, on the other hand, do not require lubrication which reduces the maintenance costs. Since oil-free compressors require no lubrication, there are also no oil costs associated with these compressors. Additionally, there is no need to purchase replacement oil filters which further reduces costs. Furthermore, oil-free air compressors are more reliable and require less maintenance than oil-injected air compressors.
This makes them more suitable for long-term use and reduces the need for regular maintenance and repairs.
Easier Operation
Operating an oil-injected air compressor is relatively simpler than an oil-free compressor. This is because the oil-injected compressor is designed to automatically lubricate the moving parts and maintain a balanced temperature during operation. With this, users do not need to worry about regularly adding lubricants or oil to reduce heat and friction. Furthermore, the oil-injected air compressor is equipped with a built-in air filter, which helps ensure a steady supply of clean air to the engine.
This prevents wear and tear on the motor and keeps the motor running smoothly for longer. On the other hand, the oil-free compressor requires manual lubrication and needs to be checked regularly to ensure that the motor runs smoothly.
Disadvantages Of Oilfree Air Compressor
Oil-free air compressors have many advantages such as lower maintenance costs and longer life, but they also have some disadvantages. One of the biggest disadvantages of oil-free air compressors is their higher initial cost. They typically cost more than oil-injected air compressors, which can make them prohibitively expensive for some.
Additionally, oil-free air compressors are generally noisier than oil-injected models, which can be a problem for those who need to use them in residential or other areas where noise is an issue. Finally, oil-free air compressors tend to produce less air pressure than oil-injected models, so they may not be suitable for some applications. Ultimately, the decision of which type of air compressor to buy should be based on the specific needs of the user.
Shorter Lifespan
Oil-injected air compressors rely on oil for lubrication, which reduces the life span of the compressor. The oil can also cause buildup of dirt and debris, clogging the air intake and reducing the efficiency of the compressor. On the other hand, oil-free air compressors do not require lubrication and are therefore able to last longer than oil-injected models.
Oil-free compressors are also less likely to become clogged and can easily run for longer periods without the need for maintenance. In addition, the life span of an oil-free compressor can be extended through regular maintenance and filter changes, while oil-injected compressors require more frequent maintenance and require more frequent oil changes. In conclusion, oil-free air compressors have a longer life span than oil-injected models.
Low Efficiency
For those in need of a reliable source of air power, two common types of compressors are available: oil-injected and oil-free models. Oil-injected compressors, while often cheaper in cost, can have a lower efficiency than oil-free compressors. This is due to the oil-injected model relying on a splash lubrication system, which can be inefficient in cooling the motor and transferring power.
This causes the compressor to lose power over time and require more frequent maintenance. On the other hand, the oil-free compressor uses an oil-free piston, which is more efficient in its power transfer and cooling functions, allowing for a more consistent performance over time. The oil-free compressor is also significantly easier to maintain than the oil-injected model, requiring less frequent maintenance.
High Operating Costs
When it comes to operating costs, oil-injected air compressors require more maintenance and incur higher costs than oil-free air compressors. Oil-injected air compressors require regular oil changes, which can be a costly and time-consuming process. Oil-injected compressors also require more frequent filter replacements, and the cost of the oil itself can add up over time.
On the other hand, oil-free air compressors require no oil changes and their filters usually last much longer. This makes them much more cost-effective in the long run. In addition, oil-free compressors often have a longer lifespan, so you won’t need to replace them as often. This helps to keep operating costs low, as you don’t need to invest in new air compressors as often.
High Noise Level
Noise is an important factor to consider when choosing an air compressor. Oil-injected air compressors tend to produce more noise than oil-free air compressors. This is because oil-injected air compressors have internal components that move and create friction, resulting in increased noise levels. Furthermore, the oil-injected system is often more powerful than the oil-free system, which can also increase the noise levels.
On the other hand, oil-free air compressors do not produce as much noise as oil-injected air compressors since there is no internal friction. Additionally, oil-free air compressors are usually less powerful, which helps to reduce the amount of noise they produce. Ultimately, if noise levels are an important factor for you, then an oil-free air compressor may be the better choice.
Conclusion
Oil-injected air compressors are typically more powerful and are able to handle more demanding tasks, but they require regular maintenance and require oil to be added to the system.
Oil-free air compressors are more economical, require less maintenance, and are better for the environment, but they are not as powerful as oil-injected compressors. Both types of compressors have their own advantages and disadvantages, so it is important to consider the specific needs of the job before making a decision.
FAQ’s
1.What Are The Benefits Of An Oil-Injected Air Compressor?
Ans: Oil-injected air compressors have many benefits. They are better sealed than other types of air compressors, resulting in reduced noise, less need for maintenance and a longer lifespan.
They also produce more air with less energy and are more efficient at cooling the air, resulting in cooler temperatures and lower operating costs. Finally, they are also more reliable and provide a steadier flow of air.
2.What Are The Drawbacks Of An Oil-Injected Air Compressor?
Ans: The drawbacks of an oil-injected air compressor include increased cost, greater maintenance requirements, and increased complexity. The oil-injected system requires frequent oil changes, and the oil must be stored and handled properly to avoid contamination and fire hazards.
Additionally, the oil-injected system is more prone to leaks than an oil-free system, leading to potential oil loss and environmental contamination. Finally, oil-injected systems are not as efficient as oil-free systems, resulting in increased energy consumption.
3.How Does An Oil-Free Air Compressor Compare In Terms Of Performance To An Oil-Injected Air Compressor?
Ans: An oil-free air compressor typically has a lower power output than an oil-injected air compressor. This means that it will not be as efficient or powerful, but it will also require less maintenance. An oil-free air compressor also tends to be lighter and quieter, making it more suitable for home use. However, an oil-injected air compressor will be more powerful and reliable in the long run.
4.What Kind Of Maintenance Is Required For An Oil-Free Air Compressor?
Ans: Oil-free air compressors do not require oil changes or lubrication, but they should be inspected regularly for signs of wear and tear. It is also important to check for any leaks in the hoses or pipes, and to make sure that the air filter is clean and free of dust or debris.
Additionally, the air compressor should be serviced as recommended by the manufacturer to ensure optimal performance and efficiency. Finally, the motor should be checked periodically for overheating, and the electrical connections should be checked for proper operation.
5.Are There Any Environmental Benefits To Using An Oil-Free Air Compressor?
Ans: Yes, there are environmental benefits to using an oil-free air compressor. Unlike oil-lubricated air compressors, oil-free air compressors do not release contaminants into the environment. Instead, they are designed to be more efficient and to use less energy while still providing the same amount of power. Additionally, they produce less noise pollution and require less maintenance than oil-lubricated air compressors.